The Saint-Etienne-based hand tool manufacturer, SAM Outillage, commits over 1 million euros annually to research and development for innovating new products. The concept of an electronically-controlled precision torque wrench emerged from this dedication—a versatile tool designed for swift and effortless deployment across various tightening operations, whether on airport tarmacs or in sophisticated assembly plants. Its core proposition lies in addressing diverse clamping needs with precision, ensuring optimized traceability of these operations, and reducing human error and physical strain on operators. Leveraging the 5G expertise of Orange Business engineers and the support of the Orange 5G Lab in Lyon-Charbonnières, this project stands as a testament to a groundbreaking evolution in the tooling sector.
SAM Outillage experimented with 5G!
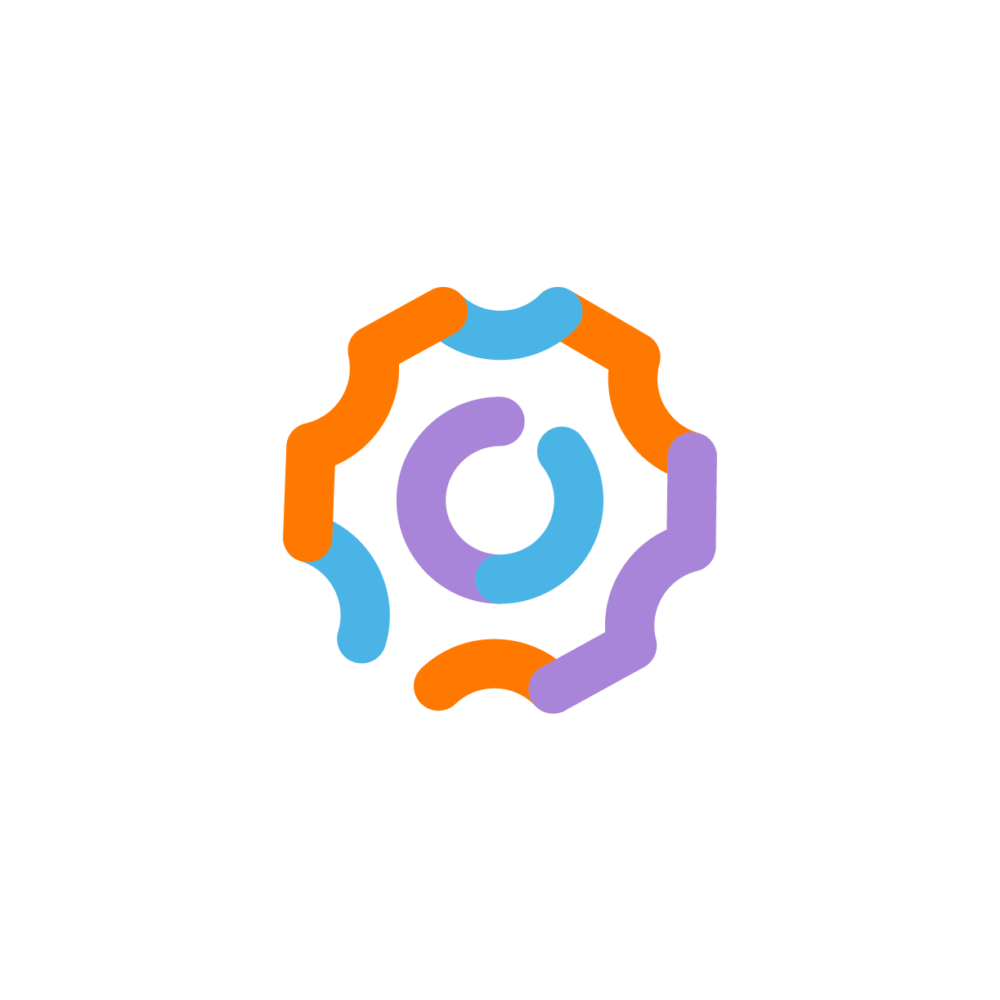
Line of Business:
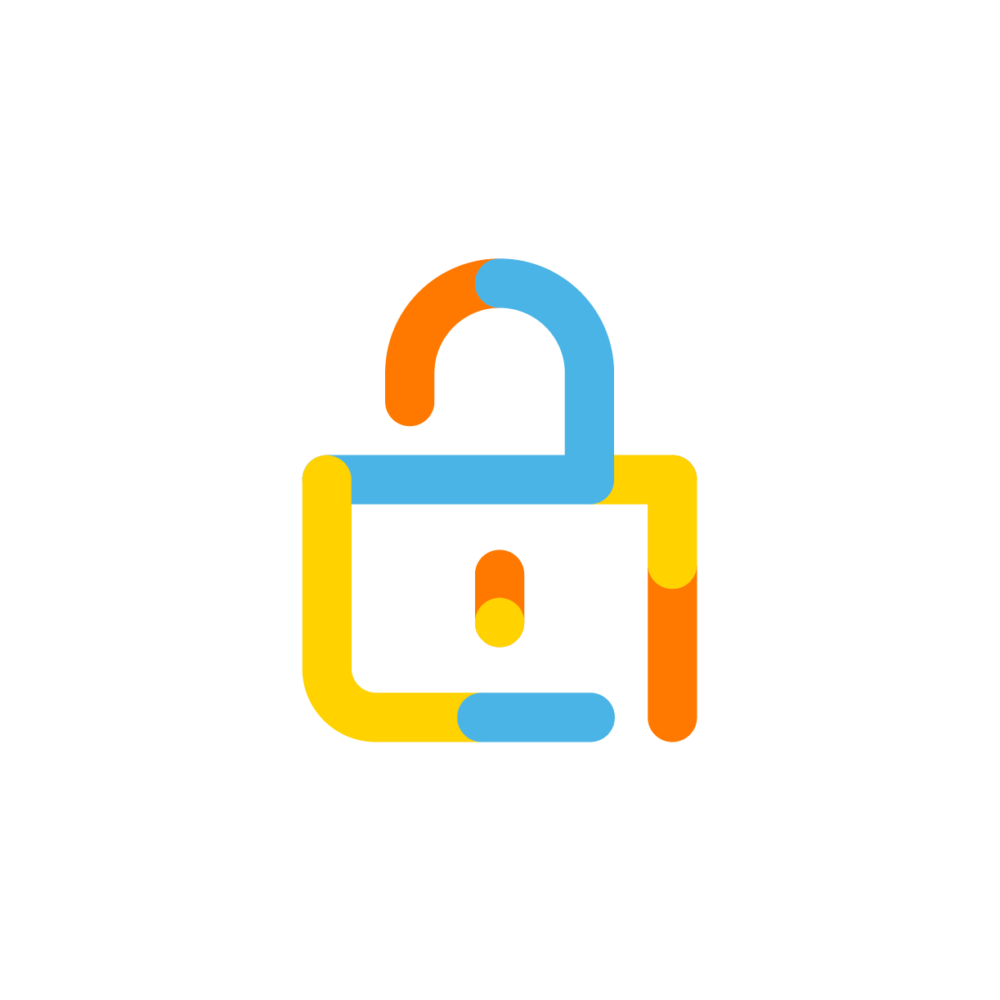
Use case
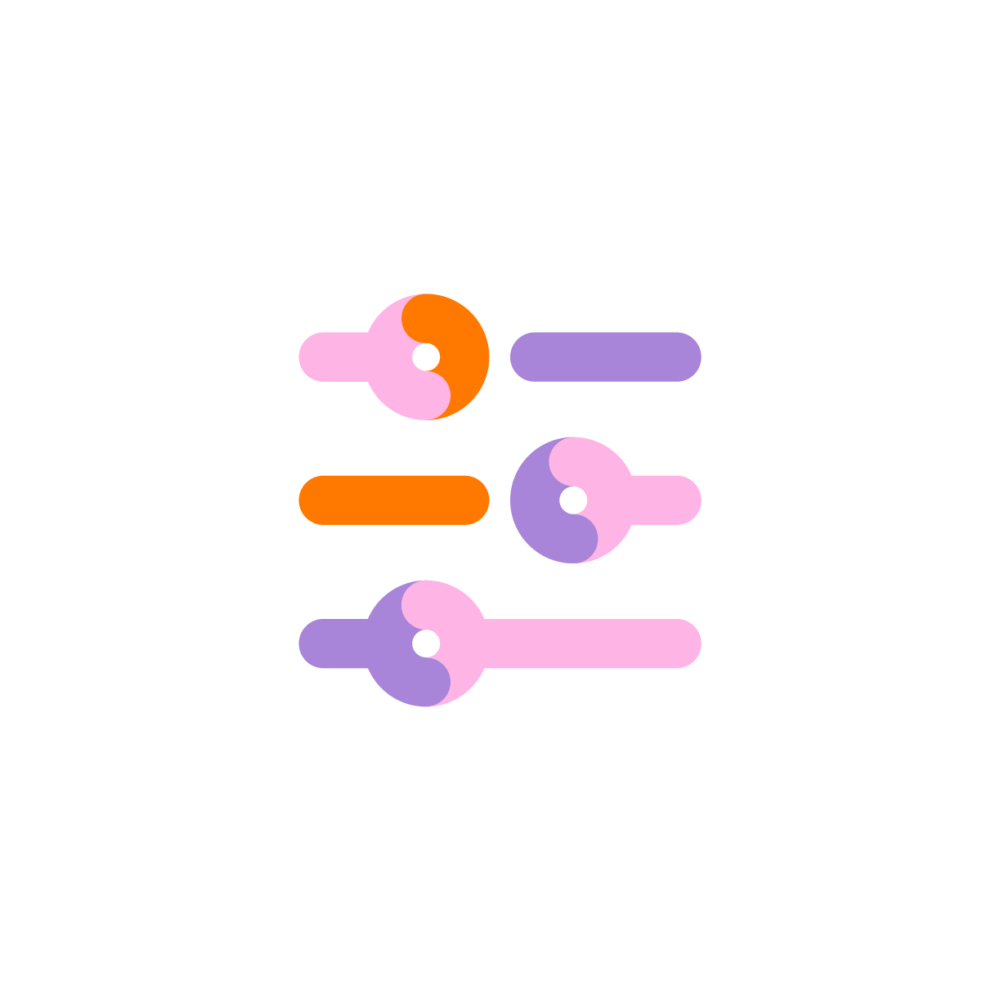
The Company’s Needs:
- Each wrench receiving precise information at its designated location.
- The interface gathering comprehensive data on all completed tightening operations, ensuring the consistency of actions.
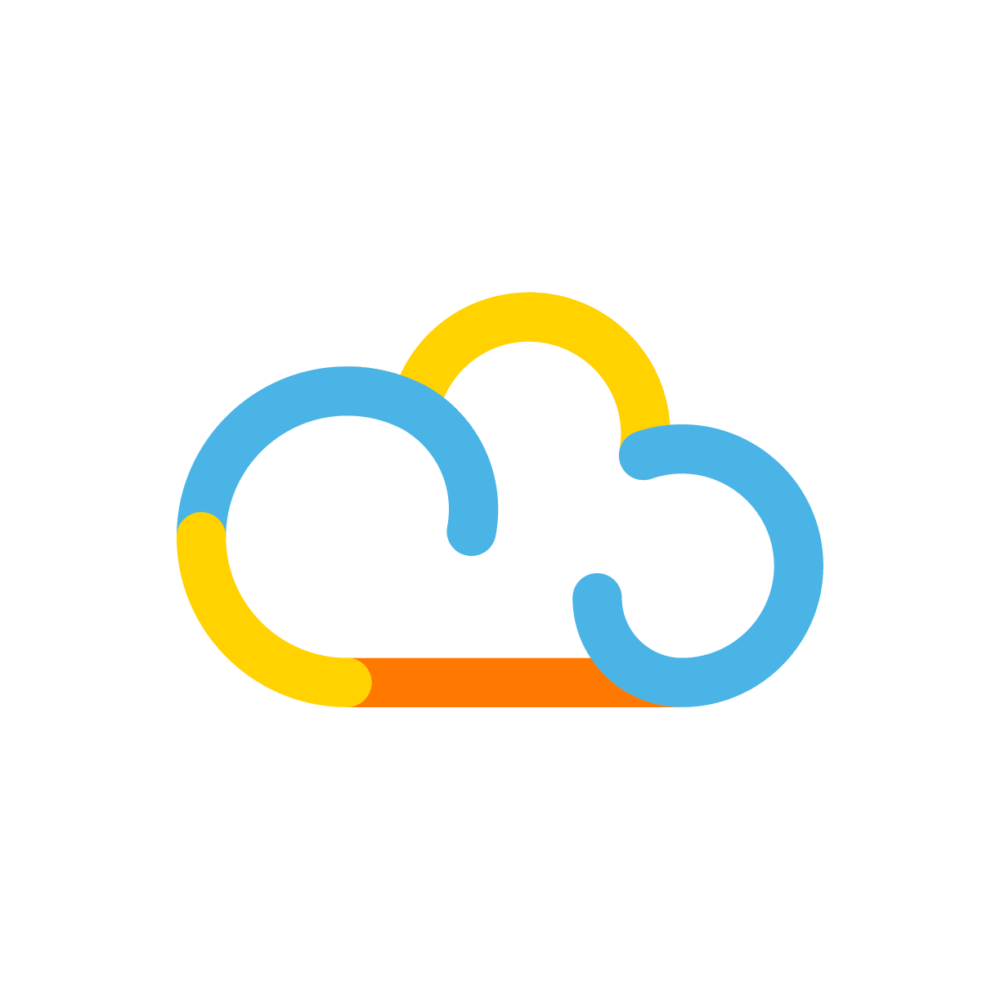
Benefits of 5G
- Low latency
- High throughput
- Stable, robust network with no downtime
- Precise geo-positioning
- No need to connect to a local fixed network
They operate in the shadows without garnering much attention. Their role is indispensable for the seamless functioning of aircraft and specialized industrial machinery. These are the maintenance workers (or operators) who diligently tighten every screw and bolt on the equipment under their care day by day. In industrial mechanics, tightening bolts is just as crucial, if not more so, than greasing bearings or changing oil. This practice helps foresee breakdowns and malfunctions, preventing production stoppages and, in the case of an airport, ensuring the successful takeoff of an aircraft. It’s not only a matter of profitability but also of safety for all users.
Industrial Tooling: A review of outmoded operations
Until now, maintenance workers tightened bolts manually, applying a precise, sometimes empirical, tightening force. This process was time-consuming and prone to errors, as the tightening depended on the operator’s judgment and physical sensation when using different wrenches. In a continuous pursuit of innovation, SAM Outillage successfully simplified a crucial part of the work for industrial mechanics operators in 2021. How was this achieved? By developing a single wrench that eliminates the need for operators to carry multiple wrenches between workstations. Lightweight and versatile, with a built-in mechanical aid, it could effortlessly tighten any bolt by simply changing the bit. Although practical, this initial version marked just a small step in SAM Outillage’s venture into the industrial tool sector.
Orange 5G Lab Lyon-Charbonnières supports SAM Outillage beyond 5G
To enhance the speed and precision of maintenance operators in adjusting each bolt, the Saint-Etienne-based hand tool manufacturer sought the expertise of the Orange 5G Lab in Lyon-Charbonnières in 2022. Situated in the Diwii/Mines Saint-Etienne Factory space on the Campus Region, this lab specializes in supporting manufacturers. Through a series of experiments and demonstrations, SAM Outillage explored how 5G connectivity could elevate performance. The Orange 5G Lab in Lyon-Charbonnières facilitated connections with two additional companies possessing the complementary technologies required for creating a distinctive tool with significant added value: Ubisense for its highly precise geolocation system and Siemens for its 5G-connected PLCs and autonomous routers.
“When SAM Outillage’s R&D Director visited the Orange 5G Lab, he not only discovered a new, faster, more efficient, and more secure network, but also witnessed the tangible prospects for development and technology,” explains Véronique Vacher, Manager of the Orange 5G Lab in Lyon-Charbonnières. “Some of these developments we have already supported and are showcasing in our premises, positioning his torque wrench as a tool of the future. Collaboratively, we partnered with Orange Business engineers to create a much more sophisticated version of this wrench. A version aligned with the current and future requirements and needs of SAM Outillage’s customers and, ultimately, an entire sector.”
Elevating performance and relevance through strategic partnership
“In early 2023, the “Operational Excellence” demo featuring the torque wrench was initiated. “We signed a partnership agreement with SAM Outillage and provided them with an Airbox 5G” continues Véronique Vacher. “With their capable R&D Development team, it was only natural for them to test 5G on their premises and explore various industrial use cases simultaneously.” Convinced of the potential, SAM Outillage returned to the Orange 5G Lab in Lyon-Charbonnières to develop, with the assistance of Ubisense and Siemens, more than just a product—an entire offering. “To automatically apply the right torque to the right bolt, the torque wrench and its operator need to be precisely geolocated. Likewise, the wrench had to be able to receive a tightening order in real-time. This is what we were able to achieve thanks to the Ubisense system, integrated directly into the torque wrench, and with the Siemens routers connected in 5G, facilitated by the Orange Business engineering teams and collaboration between the various stakeholders. Technically, this is crucial, as it is the operator, via a tablet, who translates the torque wrench tightening instructions via 5G,”
Emphasizes the manager of the Orange 5G Lab in Lyon-Charbonnières.
4G vs. 5G: the variances and advantages for manufacturers ?
Various experiments have revealed that 4G is too unpredictable for this use case.
“Micro-cuts occurred, making it impossible to precisely track the tool’s location every second.” This precision, vital for safety and production reliability in aircraft and factory machines, is now ensured by 5G. “With 5G, tooling security is a reality! Operators can work faster, as they no longer need to worry about precise tightening in specific locations. Everything is automatic and safe. In the past, the ‘news’ reported a case where a wrench was left in an aircraft engine, posing a serious risk to airport maintenance staff.”
The 5G key: enhancing reliability and inclusivity in connected tools
In detail, the 5G torque wrench revolutionizes operational safety and job appeal.
“Thanks to the driving force built into the wrench, anyone—man, woman, disabled person—can apply for this type of job” explains Véronique Vacher, Manager of the Orange 5G Lab in Lyon-Charbonnières. “No more need to carry heavy keys just in case, and no more guesswork when it comes to settings. Other tools are expected to follow suit soon.”
The 5G torque wrench can be demonstrated at the Orange 5G Lab in Lyon-Charbonnières, located at the heart of the “Region du Numérique” Campus in Lyon. The Lab is the result of a partnership between Orange, the Ecole des Mines de Saint-Étienne, and the DIWII consortium, which includes EM Lyon Business School, SIGMA Clermont, 2MaTech, SIEMENS, Human To Data, and CETIM Bosch Rexroth. This consortium aims to unite the region’s digital ecosystem and accelerate the transformation of companies in the industrial sector.
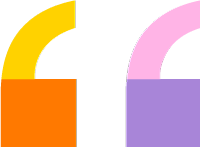
The 5G torque wrench can be demonstrated at the Orange 5G Lab in Lyon-Charbonnières, located at the heart of the “Region du Numérique” Campus in Lyon. The Lab is the result of a partnership between Orange, the Ecole des Mines de Saint-Étienne, and the DIWII consortium, which includes EM Lyon Business School, SIGMA Clermont, 2MaTech, SIEMENS, Human To Data, and CETIM Bosch Rexroth. This consortium aims to unite the region’s digital ecosystem and accelerate the transformation of companies in the industrial sector.
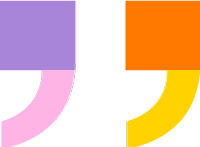
Pour aller plus loin
Et maintenant, pourquoi pas vous ?
